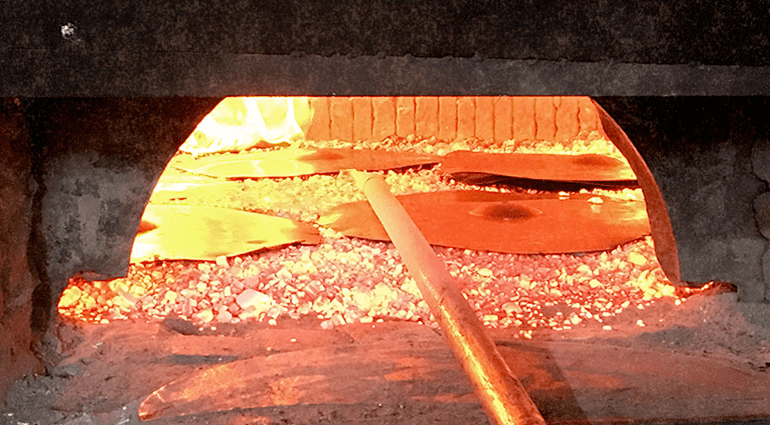
Have you ever wondered how cymbals are made and especially hand-made cymbals? It is a tough and sweaty job we can tell you that! Join us through the hot cymbal factories which make Zultan Cymbals for drummers to bash all over the world.
?
Zultan has grown into a brand with ten different series and more than 150 products. The brand has established itself on the cymbal markets and is aimed for beginners and amateurs as well as professional touring and studio drummers. This is how they are made in the hands of cymbal masters in Istanbul, Turkey.
Casting
The manufacturing of cymbals is divided into three main sections: casting, hammering and finishing. Casting itself contains four steps which we are going to explain and show you.
First we visited the factory which makes Zultan Dark Matter cymbals. When we arrived to the location of the factory we couldn’t believe how small the shop was. You could think that all cymbal factories are these big halls with mass production lines but this was something else. This little factory was only about 65 m² and only a handful of people, working hard!
The CEO of the factory said the guys work 9 hours a day and 5 days a week. We were relieved to hear that everyone in the factory knows all manufacturing processes from casting to hammering and polishing so one guy doesn’t have to spend all day in front of the oven. Even Tommi, our Finnish sauna expert couldn’t spend more than 10 seconds in front of it!
On the second day it was time to visit the factory where everything started with the Rock Beat Series. It was early morning when we were picked up from the hotel and we drove 40 minutes to the factory which was located just in the outskirts of Istanbul. This factory was bigger than the previous one because they make 5 out of 10 series of Zultan.
During the visit we got to see the casting process from the beginning. It consists of four steps:
1. Melting the bronze alloy:
The casting pots are filled halfway with boiling water so when the melted bronze is poured into the pots the “pucks” won’t get stuck in them.
2. Pressing machine and heating:
After the “pucks” have cooled just a little they go to the oven and in to the pressing machine. The pressing and oven process is repeated as many time as needed to get the right thickness for the cymbal.
- Come la pizza!
- pressing
3. Bell press:
When the cymbal has opted its right thickness it goes to a hydraulic pressing machine where the bell of the cymbal is pressed.
4. Washing and drilling:
Finally the cymbal is washed and a hole for a cymbal stand is drilled. After this they go for hammering, milling and polishing (more details about finishing later)…
Traditional Casting and Cymbal Manufacturing
We also got to see how cymbals are made honouring the traditional cymbal masters of the past. This factory is located at a 2,5 hour drive from Istanbul. This is because of their unique manufacturing process which follows the original steps of traditional cymbal manufacturing where the “ovens” are dug into the ground which is prohibited in a big city because they produce so much heat.
We arrived to the factory after a long drive and saw 4 holes in the ground and this time 2 of them were operational. There wasn’t an oven like in the previous factories and because of this it was also much hotter in there. The melting process takes time, about 3-4 hours, and they repeat this process about 3 times a day once a week. Because of this traditional manufacturing process it takes much more time to produce the cymbals than the present-day manufacturing process.
After the bronze has melted the workers lift the vessel from the ground and hang it on a rack from where the melted bronze is poured in to the casting pots one by one. In here too the casting pots are filled half with boiling water so that the bronze “puck” won’t stick in the bottom. After this the pucks are put on the side to cool off. One day of casting will provide about 40 cymbals.
Hammering
Finishing
Designing new cymbals
We also got to design new cymbals in the factories. Adrian had a certain cymbal type in mind which could be a good addition to the Zultan family. The guys in the factories immediately said “Yes in fact we can do it now!“. We were stoked by the friendliness and kindness of these people and about the fact that they were ready to provide us a cymbal we were looking for right away!
So we were testing how different hammers and milling process affect to the sound of the cymbal and modified it depending on how it sounded and came up with very interesting cymbals. Let’s see if there’s going to be a new Zultan series in the future ?
End note
By the way, all of the manufacturers of Zultan uses the scrap metal which generates from the milling to produce new cymbals so nothing goes to waste and we can preserve our planet and keep grooving ?
All in all this experience was very mind opening and it was really interesting to see how these cymbals are really made. I must give a huge shoutout and respect for these people who work in the steaming-hot factories for 9 hours a day, 5 days a week. I couldn’t handle this job for more than 1 day if I worked in those factories… These people make us drummers sound great! // Tommi Kolsi, Zultan Cymbals Social Brand Manager
We hope you enjoyed this tour of Zultan factories in Istanbul! If it was interesting and you would like to know more about Zultan make sure to follow them on Facebook and Instagram so you can keep up with the latest news, pics and videos ?
One comment
Leave a Reply
You are currently viewing a placeholder content from Facebook. To access the actual content, click the button below. Please note that doing so will share data with third-party providers.
More InformationYou are currently viewing a placeholder content from Instagram. To access the actual content, click the button below. Please note that doing so will share data with third-party providers.
More InformationYou are currently viewing a placeholder content from X. To access the actual content, click the button below. Please note that doing so will share data with third-party providers.
More Information
Hüseyin says:
Thanks for this article. I really enjoyed it. ❤